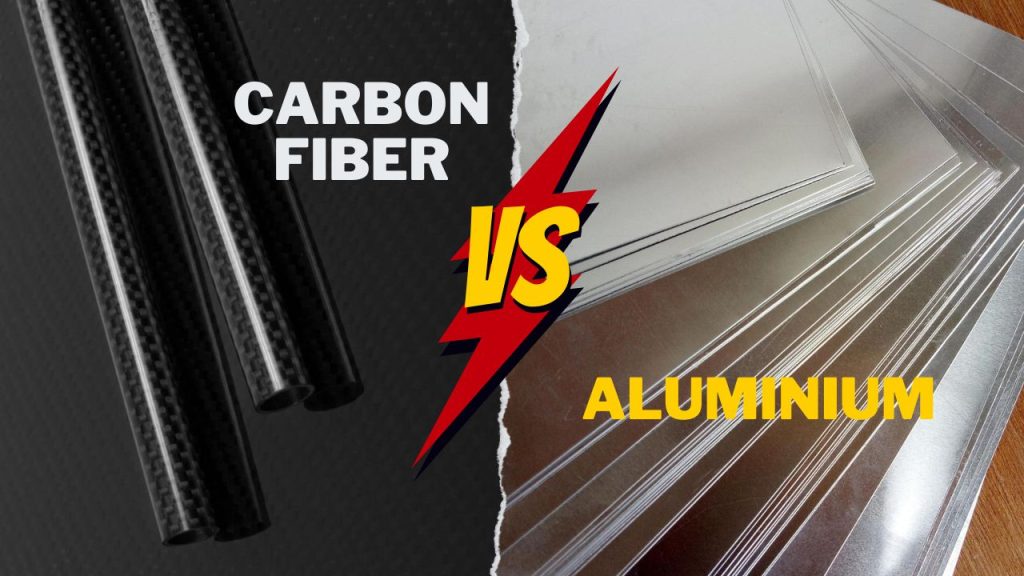
In the world of engineering and manufacturing, the quest for the perfect material is unending. Two contenders that frequently come up in discussions are aluminium and carbon fiber. Each material boasts a unique set of properties that make it suitable for different applications. In this blog, we delve into a detailed comparison of aluminium and carbon fiber, examining their strengths, weaknesses, and ideal use cases.
What is Aluminium?
Aluminium is a metallic element, renowned for its lightweight, strength, and corrosion resistance. It’s the third most abundant element in the Earth’s crust and has become a staple in various industries, including automotive, aerospace, and construction. Aluminium is often alloyed with other elements like copper, magnesium, and zinc to enhance its properties.
What is Carbon Fiber?
Carbon fiber, on the other hand, is a material composed of thin, strong crystalline filaments of carbon. These fibers are used to reinforce materials like resin to create composites. The result is a material that can be stronger than steel at a fraction of the weight. Carbon fiber composites are prized in high-performance applications, from racing cars and sports equipment to aerospace and beyond.
Comparison of Properties
Strength and Weight
Aluminium: It offers a high strength-to-weight ratio, but it’s generally heavier than carbon fiber. This makes it a good choice for applications where some weight can be tolerated, and strength is critical.
Carbon Fiber: Carbon fiber composites can be tailored to offer exceptional strength-to-weight ratios, often outperforming aluminium in this regard. This makes carbon fiber ideal for applications where every gram counts, such as in aerospace and high-performance sporting goods.
Durability and Fatigue
Aluminium: While aluminium is durable and resistant to corrosion (especially when anodized), it can suffer from fatigue over time, particularly in applications involving cyclic loading.
Carbon Fiber: Carbon fiber has excellent fatigue resistance, maintaining its integrity over many cycles of loading. However, it can be prone to impact damage and wear, especially at sharp edges or when subject to abrasion.
Cost
Aluminium: Generally, aluminium is less expensive than carbon fiber, making it a cost-effective choice for a wide range of applications. The cost-effectiveness of aluminium is particularly evident in mass-produced items.
Carbon Fiber: The high cost of carbon fiber materials and the specialized manufacturing processes required make it more expensive than aluminium. This cost is often justified in high-end applications where performance outweighs cost considerations.
Thermal Conductivity
Aluminium: Aluminium excels in thermal conductivity, making it an excellent choice for heat sinks and other applications where heat dissipation is crucial.
Carbon Fiber: Carbon fiber, in contrast, has low thermal conductivity, which can be a benefit in applications where insulation is desired but poses challenges when heat dissipation is necessary.
Manufacturing and Formability
Aluminium: Aluminium can be easily machined, welded, and formed into complex shapes, providing flexibility in design and manufacturing.
Carbon Fiber: Carbon fiber requires more specialized manufacturing processes, such as layup and curing in molds, which can limit design flexibility but allows for the creation of complex, lightweight structures that are difficult to achieve with metal.
Applications
Aluminium is widely used in automotive parts, aircraft structures, consumer electronics, and construction due to its versatility, cost-effectiveness, and good balance of properties.
Carbon Fiber finds its niche in high-performance applications where maximum strength and minimum weight are critical, such as in racing cars, high-end bicycles, aerospace components, and sports equipment.